
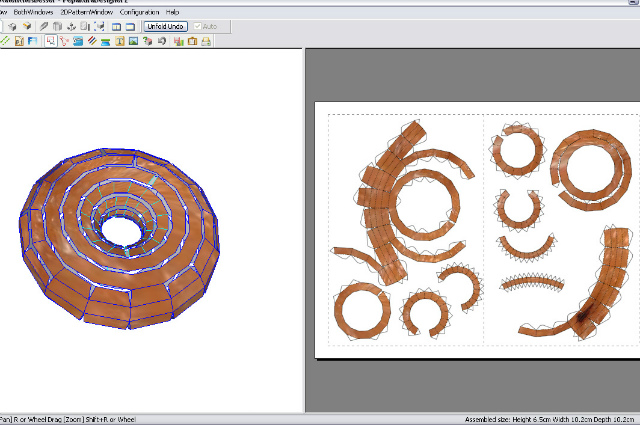
I am finally at the step of printing out my Pepakura design, and I am having a tough time with something I feel is simple. Hello everyone, i'm fairly new to using Pepakura so if someone could help me out I'd greatly appreciate it! Help Pepakura, showing edge ID and fold angles self.

Some have had good results with hot glue, especially on larger models - it is quick to set and won't cause the kinds of issues that "wet" glues have paper rippling, ink smearing. Apply glue with a toothpick and evenly spread a thin layer of it on a tab. For curved parts, it is better to curl them around a round object such as a coloured pencil or your Xacto knife handle by rubbing the object against the back of the piece. You can do this on either front of back of a piece, but front is easier. Folding - Run the back of your Xacto blade, or an empty ballpoint pen, or any similar small blunt edge along the line of a glue tab with enough pressure to leave an indent but not enough to cut it, then fold. Scissors can also be used by themselves, or together with a knife. Cutting - a self-healing cutting mat is an essential tool along with an Xacto knife or similar brand with 11 blades, or a box cutter knife.
#How to use pepakura viewer download
Then this flair is for you! If possible, please include the download link. When posting something new, use the link flair after you've made your post. Universal Conquest Wiki.Please title your posts with detail of what your model actually is low-effort titles will be removed. Sign In Don't have an account? Start a Wiki. Like all steps that utilize resins, it is important that the armor maker review procedures on ensuring their health and that of those around them, as well as preventing any damage to property.įinishing involves adding details through addition and subtraction of bondo and rondo to the outside in order to add small details that are not usually included in Pepakura models. This is accomplished by applying Bondo to the outside surface to fill the gaps between polygon edges, and then smoothing it down with sanding.
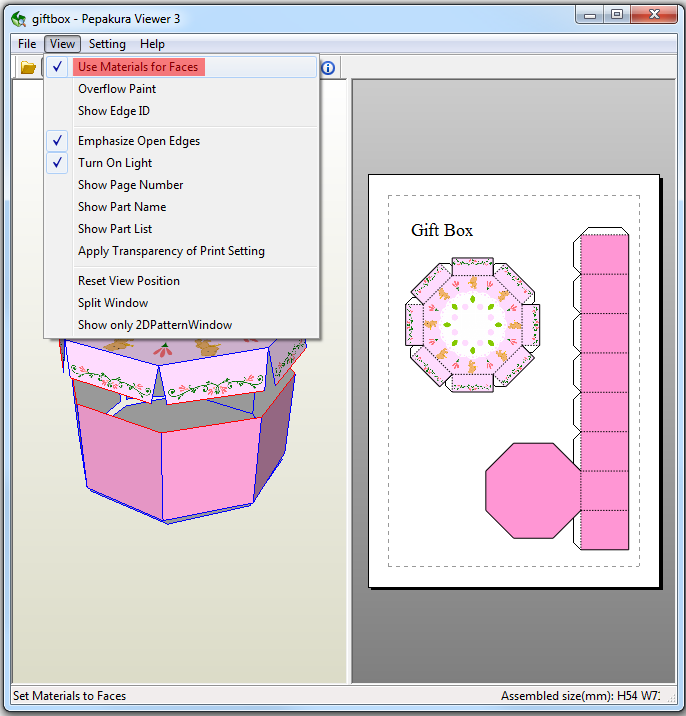
This process is to smooth over the "polygon" look the exterior of pepakura armor has in order to make it look more realistic and less like a low-resolution cg model. For information on options in other countries, look at the International Equivalents. These are ones most common for North American builders. There are a variety of materials to be used. The two most common methods are Fiberglass and Rondo, though there are many merits to combining the two. The Hardening Process is a balancing act between weight and strength, as it is difficult to get both. The hardening process reinforces it and prepares it to be strong enough to handle the Smoothing Process, as well as strengthening it to survive regular wearing. When a Pepakura object is glued together, it is still just stiff paper and is very at risk to crumpling and sagging, losing its shape. From left: Cutting board, Scoring tools pensStraight edge, Disposable scoring surface paper with marks on itGlue, Scissors, Cardstock lbs. It will branch out a bit after the pep process, but for the sake of containment, all information related to armors that begin with Pepakura will be here. This is a tutorial on the process of building armor from Pepakura to finish.
